Crane Modernizations and Upgrades
Kor-Pak provides a full scope of services designed to upgrade, modernize, and ultimately enhance your crane. Whether it be an Electrical Overhead Traveling (EOT) Crane, Ship to Shore (STS) Crane, Rail Mounted Gantry (RMG), Rubber Tired Gantry (RTG), or other industrial crane, Kor-Pak can help you take your crane to the next level for a competitive price.
Since the Industrial Revolution, overhead cranes have been put to use in a variety of diverse applications to move heavy and oversized objects that other material handling methods cannot. As your business changes with the introduction of new products or processes, so do your material handling requirements, and your existing overhead equipment may not be able to meet these demands. From the slow speeds and limited ratings of early cranes, we now find hoisting speeds of over 300 FPM, bridge speeds as high as 1,000 FPM, handling loads from 10 pounds to over 1,000 tons.
Three options exist for equipment improvement – buy a new crane, refurbish a used crane, or upgrade the present crane. There are several reasons why it is safer, more efficient, productive, and cost-effective to upgrade your existing crane.
WHY UPGRADE OR MODERNIZE?
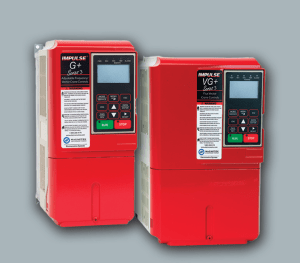
Impulse VG+ Drives
Increased production requirements may demand more capacity, faster operating speeds, better controls, or automation. Reliability may have deteriorated resulting in unscheduled shutdowns and increased production costs. Parts may be obsolete, resulting in high spare parts costs and long lead times. Inspections may show excessive wear or non-compliance with current safety standards or practices.
STRUCTURAL UPGRADES ARE COST-EFFECTIVE
The original equipment manufacturers designed the structural components of their cranes to withstand mechanical forces far in excess of those encountered in normal, everyday operations, and it is not uncommon to find overhead cranes that are more than 80 years old still in operation today. Rather than scrap an outdated crane, which is still structurally sound, it is often more cost-effective to upgrade and modify the unit to meet current operational needs.
Since the structural life of an overhead crane normally is in excess of 30 years, increasing the capacity of the crane and runway or moving the crane to another location and either stretching or shortening the span are options worth considering.
Older trolleys with their large cast iron frames, drums, gear cases, and other heavy components can be replaced with modern compact trolley-hoists, and in many cases, permit an increase in the capacity of the crane due to the reduction in trolley weight alone.
MECHANICAL UPGRADES EXTEND LIFE OF CRANE
The useful life of mechanical parts such as wheels, gears, bearings, etc. is in excess of 20 years. However, even the availability of spare parts after 10 to 15 years can be problematic. Upgrading old, worn parts with modern and improved counterparts is just one advantage to modernization.
Technological advancements in engineering can extend the life of a modernized crane. For example, modern precision gearing with much closer tolerances can result in reduced vibration, less gear wear, lower maintenance, and notably quieter operation than gears common in older cranes.
Utilizing modern Flux Vector Control and eliminating high-maintenance, inefficient hoist mechanical load brakes can improve performance, reduce wear on brake discs or pads, and allow gearing to run cooler.
One of the most important crane modernization, retrofit, or repair considerations is the

Thruster drum brake in melt shop: enduring high heat and dusty envronment
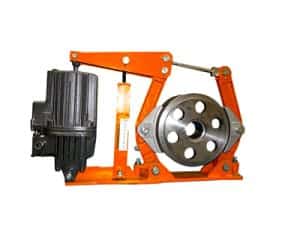
Spring-Applied, Electro Hydraulic Released Thruster Drum Brake
replacement of outdated or unserviceable crane brakes with current modern industrial braking technology.
Brake performance has improved, and brake linings last longer especially when brakes operate in conjunction with AC adjustable frequency controls or digital DC controls.
In many cases, journal bearings in pivot arms have been replaced with self-lubricating composite bearings which are shock resistant, unaffected by dirt or other contaminants, and can operate in corrosive environments. Newer brake designs include features such as automatic adjustment that compensates for lining wear and automatic equalization, which provides balanced braking and assures equal brake pad wear. These features go a long way in reducing maintenance costs and prolonging brake life.
Old hydraulic brake systems tend to leak and create maintenance and environmental issues. They can be replaced with modern “brake-by-wire” packages with foot pedal operated AC Thruster Brakes that address these issues while still providing operators with the same “feel” they had with hydraulic brakes.
Complete modern-design “drop-in” brakes are available, which meet the performance and dimension characteristics of the original equipment brakes — often at a cost less than that of a replacement component — with significantly shorter lead times. They can operate with existing brake wheels and avoid costly brake-support modifications.
Heavy Duty Caliper Disc Brakes with ratings from 50 to 30,000 ft-lbs are available as replacements for existing brakes in high duty cycle, high speed, or high torque stopping AC or DC applications.
Low cost AC Thruster Brakes are often used to replace aging DC drum brakes. These brakes eliminate the need for AC-DC rectifier panels, and have optional features, such as stepless externally adjustable time delays for both brake setting and release; external torque springs to permit maintenance personnel to “dial-in” just the right amount of stopping torque for traverse motions; and automatic adjustment and automatic equalization to reduce maintenance costs.
Motor-mounted brake-support bases can also be furnished — greatly simplifying retrofits and avoiding costly brake-support modifications.
Emergency Caliper Disc Brakes
In addition to upgrading your high-speed side brakes using thruster drum and disc brakes, you will dramatically improve the safety of your crane by adding Emergency Caliper Disc Brakes to the low-speed side of your crane. These brakes are typically packaged with a disc mounted to the flange, and Air, Magnetic, or Hydraulic Released Caliper Disc Brakes (fail safe) are selected that will provide sufficient torque to overcome full motor torque with sufficient safety factor which ultimately stops a falling load and thus precludes a major catastrophe from occurring. The emergency disc brakes are synchronized with either a PLC or Encoder which monitors the pulses of the drum and triggers the brakes to apply when the RPM reaches a predetermined amount and the brakes apply. Kor-Pak possesses the requisite experience and resources to retrofit your crane.
Storm and Parking Brakes
Storm and Parking Brakes enhance the safety of outdoor cranes, protecting it from high winds and environmental conditions that can have an adverse effect on the crane such as a Runaway Crane from occurring. Our Rail Clamps, Rail Brakes, and Wheel Clamps will hold your crane down during harsh weather conditions and ensure safety.
Gears, Rope Drums, Couplings, Wheels, and Other Products
Kor-Pak provides a full spectrum of mechanical and electrical products for your crane, including Rope Drums, Crane Wheels, Gears, Pinions, Couplings, Spreader Beams, Magnets, and other products you need. We have a complete line of new, aftermarket, and surplus products available to upgrade your crane.
CONTROL TECHNOLOGY HAS REVOLUTIONIZED CRANE PERFORMANCE
While technological advancements have significantly improved the structural and mechanical portions of an overhead crane, the process has been more evolutionary than revolutionary. What has changed dramatically, however, is how overhead cranes and hoists are controlled.
Control systems are the most important aspect of an overhead crane or hoist and without them, the machine would not function nor perform in a safe, reliable, efficient manner.
Many older cranes rely on contactors to switch regenerative load currents to resistor banks to dissipate energy. Depending upon the duty, costly contactor tips must be replaced frequently, increasing labor expense. Switching is best done with state-of-the-art AC or DC electronic controls, designed to meet current operational needs. Even owners of cranes with early versions of electronic control may have difficulty obtaining parts such as original printed circuit boards, or the manufacturer may no longer support their particular product.
The present trend toward precision handling of materials has created a demand for simple, dependable, high-performance controls — capable of communicating with computers and various other operator interfaces.
AC CRANE CONTROL MODERNIZATIONS
Perhaps no other technological development in the past 30 years has done more to revolutionize overhead crane design than the AC Variable Frequency Drive (VFD). Today’s Variable Frequency Controls and Flux Vector Motor Controls have become the industry standard for crane control. Recent improvements in drive technology, such as a new generation of Insulated Gate Bipolar Transistors (IGBTs), sensor-less vector control, powerful micro-processors with flash memory, and improved algorithms, have allowed the downsizing of the power platforms and the inclusion of many high-performance features. AC Variable Frequency Drives provide greater reliability, enhance performance, improve production throughput, prolong equipment life, and reduce maintenance costs, parts, and personnel in a variety of ways:
They reduce the characteristic high starting currents of AC induction motors, thus minimizing the shock effect on both the load and the equipment. Features, such as programmable acceleration and deceleration produce softer stops and starts, assure smooth transitions between speed steps, and greatly reduce brake wear.
THE RELIABLE AND COST-EFFECTIVE CRANE CONTROL
Crane specific software, drive support tools, and serial communication with various peripheral devices provide valuable monitoring, status, performance, and diagnostic information. Features, such as Reverse Plug Simulation, Stall Prevention, Inching Control, Micro-Positioning Control, and “Static Stepless Simulation”, are built-in and individually selectable, further enhancing the crane’s performance.
No two applications are the same. Variable Frequency Drives provide the crane or hoist user with a variety of operating modes and a wide range of options.
Most single-speed squirrel cage motors can be controlled by VFDs, including conical-rotor motors used by many European hoist manufacturers. Multiple control modes (two, three, and five step or infinitely variable speed) allow for changing the operation to suit the needs of specific applications or the desires of individual operators. A wider range of selectable speed choices (up to 1000:1) are available to the user compared to the fixed speed ratios provided by typical two-speed motors (2:1, 3:1, or 4:1) or micro-drives (10:1)
Safety is built into modern Variable Frequency Drives. They include features, which reduce the possibility of lifting an over capacity load, minimize or eliminate dangerous load swing, prevent overheating of the motor, and provide safeguards that limit unauthorized modification of drive parameters or programming unsafe parameters.
APPLICATION-SPECIFIC SOFTWARE ENHANCES PERFORMANCE, SAFETY AND PRODUCTIVITY
Simple, innovative, low-cost, application-specific software options can be added to many VFDs to meet unique application requirements and enhance performance, safety, and production throughput including Sway and Bucket Control, Drive Synchronization, and Footbrake/Static Stepless Simulation.
Sway Control improves the accuracy of load placement and reduces material damage caused by incidental contact of swinging loads without the need for external Programmable Logic Controllers (PLCs) or costly height measurement devices.
Bucket Control lets you control the various motions of a multi-line clamshell or grapple bucket that utilize two independent open/closing line hoists without the need for a PLC or master/ slave arrangement. Features such as “Bucket Position Indication”, provide the operator with the open/close status of the bucket while dredging (underwater) or when the bucket just isn’t visible; “Speed Matching” maintains the bucket in the open position while lowering; and “Torque Sharing” keeps a full bucket closed while raising.
DC CRANE CONTROL MODERNIZATION
Many find themselves today with aging overhead cranes, originally designed to perform and survive in the tough environments of steel and manufacturing plants but operating with the previous generation of high-maintenance DC motors and controls. There are some 3,000 active cranes running in North America with traditional DC controls that could be retrofitted over time. Most of these older cranes rely on traditional electromechanical DC Constant Potential (DCCP) systems which use contactors to switch regenerative load currents to resistor banks in order to dissipate the energy. DCCP systems are maintenance intensive due to their many moving and wearing parts which must operate under severe duty and in harsh environments. Rather than scrap an outdated crane, which is still structurally and mechanically sound, it is more economical to upgrade or modernize these cranes with state-of-the art electronic controls, designed to meet current operational needs.
AC is becoming the power source of choice, especially for new installations in paper mills, steel mills, bulk materials handling, shipyards, and many more areas. However, DC motors are both efficient and robust and offer year upon year of service, providing acceptable performance for the most demanding applications. Retaining an existing DC motor and upgrading the crane with solid-state controls is more environmentally friendly and – from a commercial perspective – provides an opportunity to enhance overall system performance and reliability while minimizing the risk to production and the required capital investment, an attractive proposal in today’s economic environment.
Retain existing power source, DC-motors and control wiring and replace traditional contactor control or obsolete static controls with Digital DC Controls.
OMNIPULSE ADVANTAGES
OmniPulse™ DDC & OmniPulse™ DSD
These microprocessor based, solid-state, four-quadrant DC-to-DC controls are designed for series, shunt, and compound wound motors and are a perfect drop-in replacement for
- Improved motor speed & torque control
- Minimized downtime & improved serviceability
- Reduced ongoing maintenance expenses & energy costs
- Improved safety
traditional contactor control since they easily interface with existing power and control circuitry and use the same connection points while having a smaller footprint. This is the least costly option of the three, since existing motors, brakes, and wiring can often be utilized. In addition, energy savings can be significant, since these Digital DC Controls recover energy from the load and return it to the DC power supply.
Convert crane to operate on AC power retaining existing shunt-wound dc-motors and control wiring, replacing existing controls with DC Digital Static Drives.
These drives are microprocessor digital logic controllers, which deliver precise, repeatable AC-in/DC-out control of shunt-wound bridge, trolley, and hoist motors — with reliable, energy-efficient performance — while significantly reducing operating and maintenance costs. This control has performance characteristics and many of the same advanced features of AC Adjustable Frequency Control. It can be an economical drop-in replacement for those cranes already equipped with shunt-wound dc-motors.
Convert crane to operate on AC power with low cost, efficient AC-motors and Variable Frequency Drives.
Variable Frequency Drives have revolutionized the market for high performance AC Crane Controls — now surpassing the torque control and speed regulation capabilities of DC shunt motor control.
Upgrading an aging DC crane with modern, robust and reliable DC or AC Digital Controls results in increased up-time, improved performance, reduced maintenance costs plus energy savings, which all translate into a significant return on investment
WHY USE REMOTE CONTROL TO UPGRADE YOUR CRANE?
The trend in the industry today is to operate overhead cranes from the floor rather than from a traveling operator’s cab, or in many instances, have an option for controlling the crane from either location. Because of the high cost of labor, it is more economical to remove the operator from the cab and free him up to do other tasks.
While pendant push button stations suspended from the hoist or on a separate festoon track bring the crane operator closer to the load and eliminate the need for a separate person to “hitch” or “signal”, they are often in the wrong place for safe or efficient operation, forcing the crane operator to dodge obstacles or untangle cords. Remote wireless control solves these problems.
Remote wireless control of overhead cranes and hoists has been around for over 50 years, and technology has changed significantly in recent years, allowing remote control manufacturers to bring products to market that are safer, more reliable, ergonomically designed, extremely versatile and flexible, and now affordable for even the smallest crane or hoist application.
Remote control can be transmitted by either Radio Frequency (RF) signals or by infrared light. The use of RF signals is the decidedly more popular option in the U.S., where it accounts for approximately 98% of remote control transmissions. Infrared systems, which are similar to those used for TV remote controls, have inherent problems, such as short operating ranges; frequent line-of-sight dropouts and interference from dust, bright light, and sunshine; and relegation by the leading US manufacturers to down-load/up-load functions.
Modern Radio Remote Controls employ state-of-the-art technologies such as Graphic Displays and various types of wireless communication including Synthesized Frequencies, Time Multiple Sharing and Frequency Hopping Spread Spectrum (FHSS).
n Graphic Displays are now available on many systems offering system diagnostics including battery life, signal strength, and warning symbols; and two-way RF for applications requiring feedback of crane parameters, alarms, and command confirmation.
Radio Products
FLEXIBLE. DURABLE. POWERFUL.
- Ergonomic, lightweight designs
- Rugged, chemically resistant cases
- Programming flexibility and customizability
- Graphic displays with system diagnostics
- Wide selection of RF ranges and frequency options
- Maximized power efficiency
The use of electronically Synthesized Frequencies eliminates fragile crystals and permits easy reconfiguration of transmitters. Time Multiple Sharing allows up to four systems to share the same channel without interference.
Frequency-Hopping Spread Spectrum (FHSS) allows the system to communicate relatively interference free by sending RF messages over multiple frequencies many times a second, seeking the clearest channel, thus avoiding the risk of interference on a single frequency. Spread Spectrum technology also offers the opportunity for applications that require transmitting and receiving over long distances, up to 3,000+ feet.
The flexibility in programming inherent with these technologies means operators can customize output configurations, frequency channels, and security codes via a PDA or laptop computer or self-configure systems through infrared or other communication links.
Consequently, one spare transmitter can be easily reconfigured by the user for application on a multitude of systems without opening the case and flipping dip switches.
These technologies, when used with the latest microprocessor technology, such as I-Chips, flash memory, and surface-mounted printed circuit boards, combine to provide the ultimate in reliability, flexibility, versatility, safety, and performance for the remote control crane user.
WHY MODERNIZING WITH AUTOMATION?
Technological advancements in control products and engineering have enabled us to convert outdated manually controlled overhead cranes, hoists, and monorail systems into modern production tools with an extended life cycle.
The automated material handling system, for example, offers a wide range of benefits including space savings, lower building costs, improved productivity, more efficient material flow, accurate positioning, fewer personnel required, safer operations, reductions in inventory, increased reliability, reduced operating costs, and better return on investment (ROI).
In addition to improving production and reducing costs, the trend in automation is also to focus on broader issues such as increasing quality and flexibility in the manufacturing process.
Highly developed solid-state logic and computer-regulated control systems define what automation is today. Flexibility and networking capabilities of Programmable Logic Controllers (PLCs) and other computers allow easy integration of related systems. They can be linked to production management computer systems, thereby providing better inventory control, improved process control, and feed-back of important management data on the operation.
Existing overhead cranes are routinely interfaced with automatic guided vehicles, conveyors, stacker cranes, and monorails for increased efficiency.
The ability to integrate standard components such as Variable Frequency Drives with their built-in innovative electronic control functions has revolutionized the industry and driven down the cost of automated systems. Variable Frequency Drives not only provide speed control but can aid in positioning.
The Kor-Pak Advantage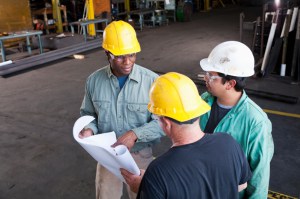
Kor-Pak leverages its engineering, experience, and supply chain to provide outstanding Crane Services and will successfully assist you in your Crane Upgrade and Modernization projects. Additionally, Kor-Pak provides Crane Inspections and Training Services, Commissioning, Repair and Remanufacturing of existing equipment such as gearboxes, brakes, controls, and motors. Kor-Pak also manufactures and distributes hundreds of spare parts for crane equipment and can provide expedited lead times and competitive prices. Contact a Kor-Pak representative today to begin your next crane upgrade and modernization project.
For more information, Contact a Kor-Pak representative today.